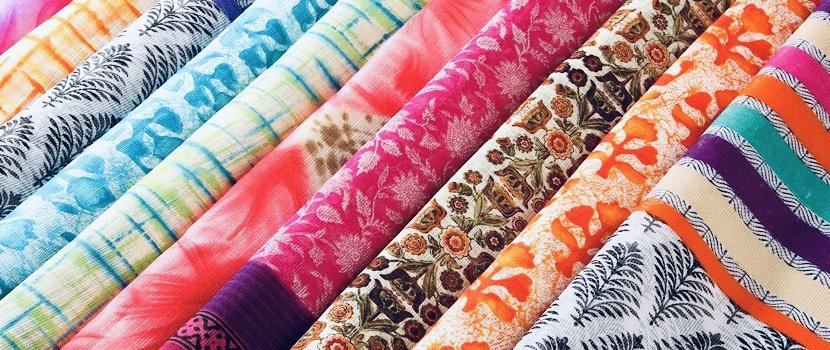
Ever wondered how those vibrant patterns on your favorite shirt or curtains come to life? Welcome to the colorful world of printed cloth, where creativity meets technology to turn plain fabric into wearable art. From ancient block printing to today’s digital wizardry, the process has evolved over centuries, blending chemistry, engineering, and imagination. So, how does a blank textile become a masterpiece? Let’s walk through the fascinating journey of fabric printing—and peek at the innovations shaping its future.
Step One: Prepping the Canvas
The magic of printed cloth starts with preparation. Choosing the right fabric is key—cotton, polyester, silk, or blends each bring unique traits that affect how they take ink. Cotton loves dyes, polyester shines with sublimation, and silk offers a luxe base. Once selected, the fabric gets a makeover: scouring strips away oils and impurities, bleaching creates a clean slate, and mercerizing (for some) boosts shine and dye uptake.
Why all the fuss? Skip these steps, and you risk blotchy prints or colors that fade fast. It’s like priming a wall before painting—tedious but essential for crisp, lasting designs. With the fabric prepped, it’s ready to soak up the artistry ahead.
Designing the Dream: From Sketch to Screen
Next comes the fun part—creating the design. Textile artists dream up patterns, drawing on trends and flair, then bring them to life with digital tools. Software lets them tweak colors, sizes, and repeats with precision, turning ideas into printable blueprints fast.
Once finalized, the design gets split into color layers—each hue needs its own turn in the printing process. Then, screens are crafted: traditionally silk, now often polyester mesh, stretched tight and coated with light-sensitive emulsion. UV light hardens the pattern onto the screen, leaving a stencil for ink to flow through. Flat screens suit small runs; rotary ones speed through rolls. It’s a blend of art and science, setting the stage for the print to pop.
Bringing It to Life: Printing Techniques
Now, the design hits the fabric—and there’s more than one way to do it. Screen printing, a classic, pushes ink through those stencils onto the cloth. Flatbed screen printing nails intricate details for limited batches, while rotary cranks out yards at high speed. Digital printing, the modern kid on the block, uses inkjet tech for photo-realistic precision and endless colors—perfect for custom jobs or small runs.
Then there’s block printing, an old-school gem. Artisans carve wooden blocks, ink them up, and press them by hand for a crafted, one-of-a-kind vibe. Each method has its edge: screen for bold runs, digital for flexibility, blocks for charm. The choice hinges on fabric, design, and scale—polyester might get sublimation heat-transfer, while cotton loves a good screen.
Coloring the World: Dyes and Pigments
What makes those prints sing? Dyes and pigments. Dyes bond chemically with fibers for fade-resistant color—reactive dyes for cotton, disperse for polyester. Pigments stick to the surface with binders, offering more shades but less durability. Matching the right colorant to the fabric is crucial for vibrancy that lasts.
Mixing exact hues takes skill and tech—color-matching software helps nail the designer’s vision. Sustainability’s stirring the pot too, with eco-friendly dyes cutting chemicals and water waste. From bold reds to green innovations, these unsung heroes define the look and life of printed cloth.
Finishing Touches: Locking It In
Printing’s just the start—post-processing seals the deal. Drying sets the ink, preventing smears, with options like heat tunnels or air drying tweaking the finish. Curing follows, bonding colors to fibers via heat, steam, or chemicals—skip it, and your print might wash away.
Extras like softeners or water-repellent coatings boost feel and function, while eagle-eyed inspectors catch flaws in color or alignment. These steps turn raw prints into durable, polished textiles, ready for your closet or couch. It’s the unsung work that makes the magic last.
Looking Ahead: The Future of Fabric Printing
The journey of printed cloth is a tale of evolution—and it’s far from over. Sustainability’s driving change, with water-free dyeing slashing environmental impact. Digital printing’s speeding up, hinting at a future where you might design and print custom fabric from home. Smart textiles are on the rise too—imagine shirts with printed sensors or patterns that shift with a tap.
Then there’s 3D printing, crafting seamless garments to fit you perfectly, and nanotechnology weaving in stain resistance or color-changing tricks. Bio-based inks from algae promise greener hues, while augmented reality could layer dynamic designs onto fabric via your phone. The possibilities? Endless—and thrilling.
Why It Matters: The Printed Cloth Story
From prepping fabric to futuristic trends, printing cloth is a dance of tradition and innovation. It’s how a blank bolt becomes a bold statement, blending meticulous prep, clever tech, and vibrant color. Whether it’s screen-printed tees, digitally crafted scarves, or hand-blocked treasures, the process delivers beauty we live in daily.
What’s next? A world of greener, smarter, more personal textiles. Picture clothes that monitor your health, curtains that cut waste, or patterns you dream up yourself. The art of printed cloth keeps evolving, inviting us all to wear, use, and imagine more. What design will you spot—or create—next?